

In the coated samples, all it took was a 100 micron-thick polymer coating to provide the parts with up to 4.5x more resistance to catastrophic fractures. Even when pushed to the point of breakage, the coated structures didn’t completely explode, crumbling and flattening instead. “We’ve clearly seen that the uncoated structures are very brittle,” said Rahman.

“But when we put the coated structures under compression, they will take the load until they completely break. And interestingly, even then they don’t completely break into pieces. They remain enclosed like laminated glass.”Īdditionally, when compared to coated solid ceramic materials, the porous 3D printed schwarzite lattices were determined to be inherently tougher. This was attributed to the mechanism by which the polymer coatings infused into the porous structures, ‘filling up’ the pores to improve density and mechanical resistance “The architecture definitely has a role,” explains Seyed Mohammad Sajadi, lead author of the study. “We saw that if we coat a solid structure, the effect of the polymer was not as effective as with the schwarzite.”įurther details of the study can be found in the paper titled ‘ Damage-tolerant 3D-printed ceramics via conformal coating’. It is co-authored by Muhammad Rahman, Seyed Mohammad Sajadi et al. Uncoated and coated ceramic schwarzites under a hydraulic press. Photos via Rice University.Ĭeramic 3D printing has applications in all manner of fields and industries. Earlier this year, researchers from Shenzhen University and the Southwestern Institute of Physics developed a means of additively manufacturing ceramic structures that emit nuclear reactor fuel.
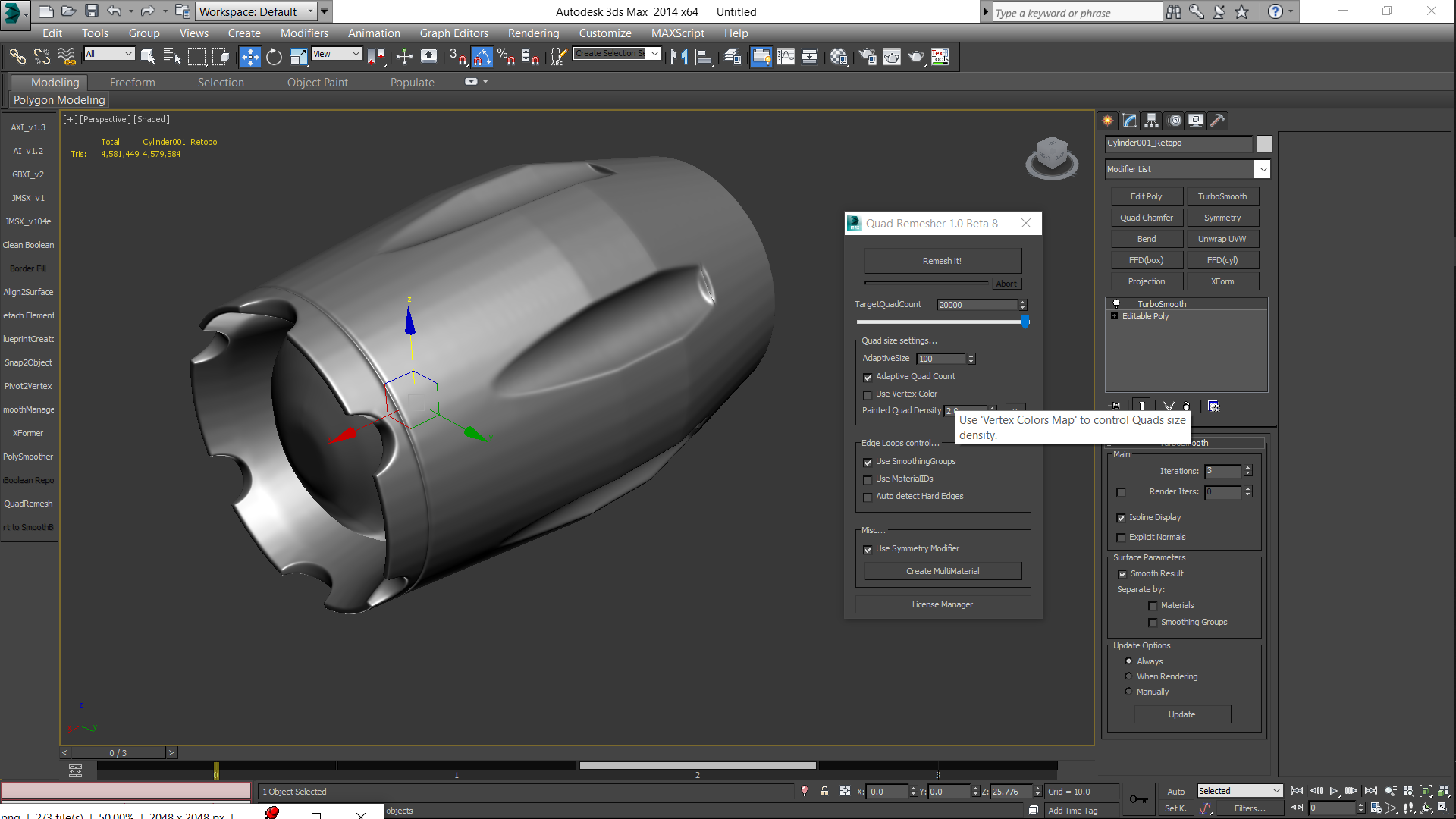
Utilizing lithium-loaded ceramics and DLP 3D printing, the team was able to create ‘breeding blankets’ that self-sufficiently generate tritium, a vital element of the nuclear fusion process.Įlsewhere, in the medical field, scientists from the Skolovo Institute of Science and Technology have previously developed a novel method of 3D printing personalized ceramic bone implants. Specifically, the team deployed a simulation-based approach to create flexible, flaw-free 3D models that could be used to print porous implants. Nominations for the 2021 3D Printing Industry Awards are now open, have your say in who is leading the industry now. Subscribe to the 3D Printing Industry newsletter for the latest news in additive manufacturing. You can also stay connected by following us on Twitter, liking us on Facebook, and tuning into the 3D Printing Industry YouTube Channel.
